![[Translate to English:] Batterietestzentrum Gebäude](/fileadmin/_processed_/0/a/csm_bst_gebauede_69d0e14e3c.png)
Since 2014, the Fraunhofer HHI in Goslar has been operating a test center to characterize and validate the thermal and electrical behaviour of lithium-ion battery systems under various operating conditions. The focus is on scientific investigations into battery safety, extinguishing agents, fireproof materials and innovative sensor technology and diagnostics. The test center also offers services for industrial partners - for example, long-term cycling of cells, modules and systems in climate chambers, thermal fuse tests of battery systems with capacities of up to 150 kWh or extinguishing agent tests under defined conditions. The Fraunhofer HHI offers unique diagnostic options such as fiber optic temperature and strain measurement. Certifications can be carried out with appropriately accredited partners if required. The test center is ISO 9001 certified and TISAX certification is currently being processed.
All tests and investigation methods for lithium-ion batteries (NMC or LFP chemistry) can be easily transferred to new types of batteries such as sodium-ion batteries and are already being successfully carried out at the test center.
Another focus of the Fraunhofer HHI is the development and subsequent provision of sensor systems for reliable characterization and early identification of safety-critical conditions. In addition, safety concepts such as energy-consuming separation layers, extinguishing systems, gas neutralization filters and emergency shutdown systems based on active and passive components in a controlled environment are being developed to application maturity in order to provide the necessary safety features for critical infrastructures, 2nd life energy storage systems and prototype batteries.

Equipment overview
Scienlab Battery Test SystemSL60/600/36kW
SL60/200/12BT4C
SL60/300/18kW
AVL - Power test bench for electrical load tests
Electrodynamic Shaker Data Physics V13-33/DSA5-15K
| Fuelcon Evaluator-B
Sécheron short-circuit tester |
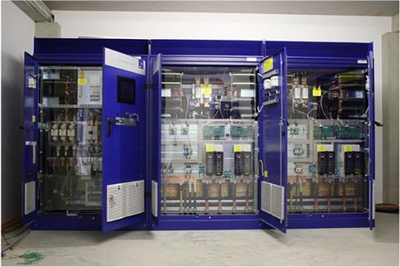

Services
In addition to research and development work on battery safety and condition characterization, Fraunhofer HHI provides the following services:
VDE-AR-E 2510-50:2017-05
| ECE R100
UN 38.3
|
* Up to approx. 150 kg resp. 25 kg
** Can be realized short-term after consultation
Reference
![[Translate to English:] Brandofen fuer Batterien](/fileadmin/_processed_/2/2/csm_Gesamtanlage_batterietestzentrum_67a4db39bd.jpeg)
- TÜV Rheinland
- Brandschutz Voß GmbH
- Power Innovation GmbH
- Volkswagen Aktiengesellschaft
- Porsche Engineering Services GmbH
- FLN Feuerlöschgeräte Neuruppin Vertriebs GmbH / Johnson Controls
- REMONDIS Industrie Service GmbH & Co. KG
- Hoppecke Batterien GmbH & Co. KG
- Intilion GmbH
- ElringKlinger AG
- VoltaLabs GmbH
- FOGTEC Brandschutz GmbH